Three Types of Construction Estimating Techniques
(…Everyone Uses Whether They Know It or Not)
There are a gazillion types of software, programs, catalogs and/or other tools for estimating construction costs. But all of these price-delivery tools fall into one of three basic categories.
- Analogous
- Parametric
- Bottom-Up
What do these mean? How are they used? Which one should you use?
Glad you asked.
Analogous Estimating
Analogous estimating (sometimes also called top-down estimating for reasons you’ll understand in a second) is a form of experienced, sophisticated guess-estimating. It’s also the handiest and least detailed.
Analogous estimating relies on experience. Cost information is derived from historical information from previous, like-kind projects. The projects need to be similar only in broad categories such as size, project schedule, industry type, (manufacturing, distribution, bio-tech, lab, etc.) and the type of the constructed or installed improvements.
For example, let’s say you’re using the Analogous estimating technique for a life science lab. Start by drawing on cost information that you have archived from previous similar projects. This would include mechanical, electrical, lab equipment, benches, finishes and flooring etc. Assuming the projects are similarly sized, an estimator could “analogize” the cost of the previous projects to the present example.
Architects and engineers are likely to select this type of estimating methodology.
This works well if the projects are similar in many broad dimensions. What the Analogous method lacks in specificity or detail it makes up for in speed and convenience.
Parametric Estimating
Parametric estimating introduces a bit more empiricism. While not detailed down to every nut and bolt, it does rely on algorithms and mathematical relationships to establish cost.
Parametric estimating relies on the mathematical relationship of cost per unit. The unit can be square footage or length of cable or number of outlets or linear footage of wall. The point is that manageable chunks of the work are assigned labor and material costs. These unit costs are then multiplied by the quantities in the particular project.
Parametric estimating provides a much more higher level of accuracy and sophistication. As long as the underlying data is up to date and accurate, one can get high quality estimates without the tedium of counting every single carpet fiber.
While not as solid as Bottom-Up estimating, Parametric estimating is a great way to get a semi-solid estimate of costs without the brain damage and time required for a complete Bottom-up estimate.
Bottom-Up Estimating
This is the methodology used by almost all general contractors.
Bottom up estimating is a detailed quantity and labor take off. Materials and tasks are broken down into the smallest reasonable component.
Let’s take light fixtures for example. Imagine a matrix of every light fixture to be installed on the project. Naturally each light fixture would have an individual cost multiplied by quantity. Similarly each fixture would have a associated amount of time for installation. Multiply the number of fixtures by the time by the fully loaded cost of labor to install the fixtures and voila!, you’ve got a powerful, detailed component of the larger cost estimate.
Then basically rinse and repeat for every other element of the project.
This technique is embodied in a broad range of construction estimating software and books. But generally speaking, they’re all just automating or more efficiently executing the technique above.
This technique is essential, maybe even mandatory for competitive bid situations. On the other hand, if time is of the essence and the scope of the project is still a bit fluid, an Analogous or Parametric estimating technique may be more suitable.
Bottom Line (no pun intended)
It’s less important which of these methodologies you choose as long as you’re aware of what you’re getting.
A conceptual budget to provide a broad framework of the total cost of the project may be effectively accomplished with Analogous estimating. However in a competitive bid situation expert professionals, regardless of the software or tools, will perform some variation of Bottom-up estimating.
As long as the choice is informed and deliberate, each estimating technique has its place depending on the trade-off between speed and accuracy.
Either way there’s no substitute for experience. I’m reminded of the old saying, “Good judgment comes from experience and experience comes from bad judgment”. Choose wisely my friend.

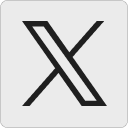


