Scheduling Projects: How Top Project Managers Do It Differently
Why is that?
“The software lets the end user do too many dumb things,” says Jonathan Japka, a civil engineer by training and consultant on project management scheduling. “Most of the people who are practicing scheduling have never been formally trained, and they don’t know what a good schedule or a bad schedule is. I always put the question to [schedulers] by asking, how did you learn? It’s usually by mentors.”
The influence of software tools on scheduling confusion continues to be a flashpoint in construction—especially over how “float,” the extra time for activities, can be calculated or manipulated.”
The problem is exacerbated at many companies because they tend to hire PM’s who know the software, but have no practice experience or haven’t been properly trained on construction techniques. They don’t understand the time and coordination needs of the various trades, Japka said. He continues:
“There are several trades that often just need one trade to get a few days’ head start on the successors, such as metal-stud framing followed by electrical in-wall rough-in. The electrician is not going to wait until framing is complete to start. But at the same time, wall framing needs to complete before electrical in-wall can complete: SS-FF. And in most cases, there is no practical way (or useful purpose) to break down the framing activity any further to create an opportunity for a FS relationship. Are some of the lags going to be somewhat subjective? Yes. There is no way around it. But it is realistic because, at some point, there will be a subjective decision on when the electrician will start.”
So what’s the solution? In our experience, it’s hiring a project leader who is master of both the construction process and the software tools that help line up each task and timeline requirement for maximum efficiency and cost savings.

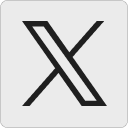


